Drilling Holes
(Oh how I LOVE to drill holes! Lots and lots and lots and lots and
lots and lots of holes...)
By the time I was finished I drilled 9,116 holes not counting however
many holes got drilled in fixtures that were rejected after the holes were
drilled. If a fixture is going to be rejected it's a lot better to
find out before drilling holes in it. Magnet-mounting holes are drilled into a pair of
fixtures at a time. But the accessory holes are drilled
one hole at a time in individual fixtures for maximum
accuracy.
I begin by drilling the magnet-mounting holes. These holes are two
sizes with the forward hole (and middle hole in six-magnet fixtures) being
larger than the rear hole to allow the fixture to be squared 90°
to the building board.
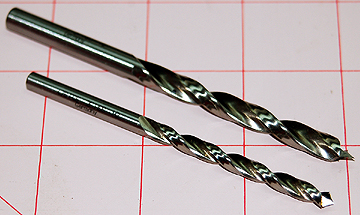 |
These
are German made brad-point drill bits. They are somewhat expensive but
last longer than the brad points I've purchased at local hardware stores
making them worth the investment.
A close up of the drill bit tips.
|
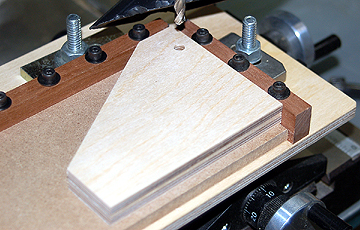 |
I started with the rear hole. The drill press is
set up and tested using a rejected fixture before drilling the good
fixtures. The
fenced table I made for my Microlux X-Y table (compound table) allows very accurate drilling.
It's a small table but very appropriate for what I do. I have
looked for larger tables to use with my larger drill press but they are
very heavy and I doubt the drill press table could support the ones I've
seen.
Compound tables are generally intended for use with milling machines,
not drill presses. They can be used with a drill press but the
drill press table needs to be able to support the weight.
All
done.
|
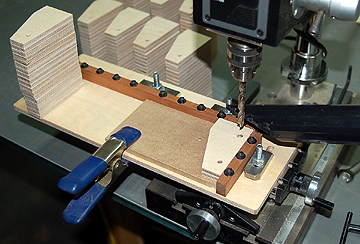 |
Next I drill all the front holes. Because the front
and rear holes are centered the exact same distance from the bottom and
the front or rear of the fixture all I need to do is change out the bit,
test drill one of the rejects and start drilling if everything is ok.
All
done. |
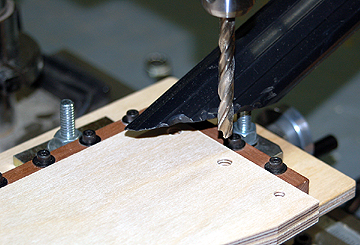 |
Finally the center magnet-mounting holes are drilled
in all six-magnet fixtures and that completes the drilling of
magnet-mounting holes.
All
done.
I won't be drilling any fixture holes using my miniature drill press in
the future. I built a mount so I can install this X-Y table on my
larger bench top drill press which is more suited to production work.
In fact, I strongly recommend that you do not buy the drill press shown
here. I will be writing about it elsewhere on this site and when I
get to it there will be a link from here so you know why you shouldn't
buy it. |
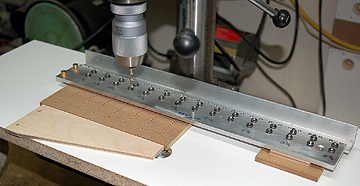 |
Now it's time to get serious about drilling. A
repeating pattern of mounting holes is drilled to allow the mounting of
various accessories such as Vertical Presses and Press Bridges.
This drill jig was made by my machinist friend Joe Tabajdi.
This jig is aluminum with fifteen pairs of hardened steel drill bushings
pressed into place. There is a forward fence and two brass rod
stops at the bottom of the jig. Every fixture is placed against
the fence and the stops which results in an identical hole-pattern on
every fixture. It's a beautiful thing because it allows items such
as bridge presses to be mounted to fixtures which do not have to be the
same size. |
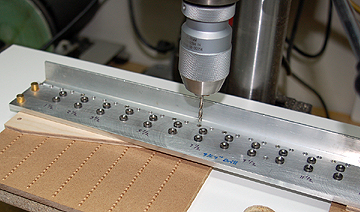 |
The fixture is placed on a sacrificial backer board.
The jig is placed over the fixture, properly aligned and held in place
while the first hole is drilled in one end of the fixture. |
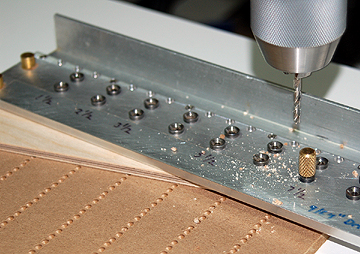 |
A steel pin is inserted into the drilled hole to maintain
alignment between the drill jig and the plywood fixture. |
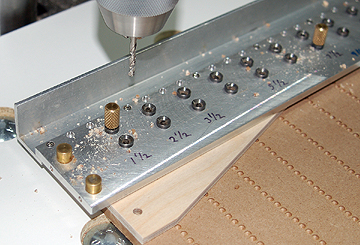 |
A hole at the opposite end of the fixture is drilled and
also pinned. |
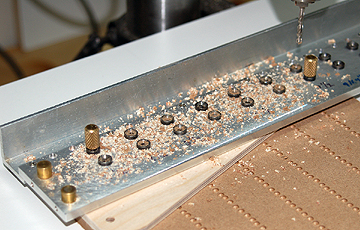 |
Now that the plywood fixture is secured to the drill jig
the rest of the holes are drilled. |
I have purchased just about every drill bit available to
achieve the cleanest holes possible. Some of those bits were very
expensive such as solid carbide and cobalt bits. Those bits chipped
very easily when they struck the hardened drill guides which is something
high-speed steel twist bits didn't do. It's not easy lowering
the bit dead-center into the guide hole thousands of times.
I didn't think brad point bits would work because any time the bit hit
the drill guide it would quickly dull the bit. As it turns out the
brad point bits available in this size just don't work very well anyway.
I tested brand new bits on scrap plywood without using the drill jig and the
brad points just didn't work. There was significant tear-out on the
underside of the wood.
Surprisingly the best quality hole is drilled by the least expensive high
speed steel twist bit. These bits only last for about 150 holes before
they start tearing out the bottom of the hole at which point I discard the
bit and replace it with a new one. New bits cost less than the charge
to resharpen them. I've looked into drill bit sharpeners but these
bits are on the bottom end of the range that can be sharpened and my
experience is that no tool works very well when close to the extremes
of the stated range. Plus none of these tools have received reviews
that made me want to purchase them.
I suppose I could spend tens of thousands of dollars buying whatever tool
the drill bit manufacturer uses but at the little over a dollar I pay for a
bit now I don't think I'd ever break even.
One last thing I learned in all my experimenting —
not all drill bits the same size are the same size. One manufacturer's
9/64" can be quite a bit different from another's as is evident when putting
the same bolt through holes drilled by different bits.
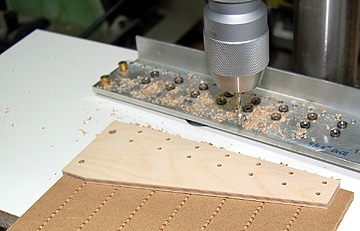 |
A 7-1/2" fixture having all accessory holes drilled.
All
done.
Obviously this is a very time-consuming step and I'm always glad to
get to the point where I'm not standing in front of the drill press for
hours every day. |
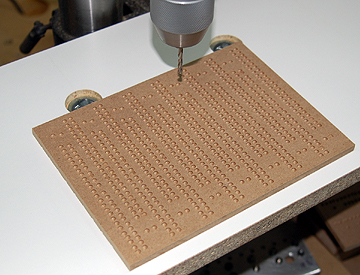 |
I figured out a system of placing each fixture on the
backer board quickly to ensure every hole is drilled in a new spot while
using as much of the board as possible. Each backer is used on
both sides. I cut them from 1/4" MDF which is very
inexpensive at about six bucks plus tax for a 2' x 4' board. It
only took a short time to cut down a board into a lot of backer boards. |
|